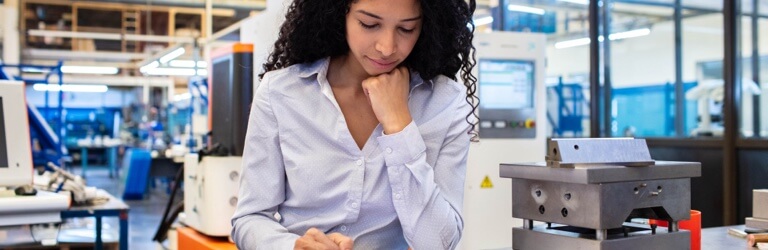
Why you should consider switching to lean manufacturing
Running a manufacturing business, like any other, incurs costs. To optimise profits, companies must search for ways to reduce these costs relative to income. One of the latest trends in the sector is the adoption of lean manufacturing.
What is lean manufacturing?
Lean manufacturing (also known as lean manufacturing software) is the use of tools and processes to help reduce waste in all business processes through the use of big data and incremental improvements, thereby improving efficiencies and productivity, and making your business processes more effective and, ultimately, more profitable.
The driving force behind this need is customers’ increased expectations for short lead times for products made exactly as specified and delivered on time, every time.
The ability to quickly respond to changing customer demands requires the use of manufacturing systems that can be reconfigured and expanded then and there. It also needs to accommodate advances in assembly techniques without making initial manufacturing investments obsolete.
Lean manufacturing is an operational system that:
- maximises added value,
- reduces essential support and
- eliminates waste.
Lean production is the implementation of the concept that anything that does not create value in the product is to be eliminated, producing more value for less work. ”
How can I start to implement lean manufacturing in my business?
To begin implementing lean manufacturing in your business, you need to follow these 7 principles:
- Eliminate waste: reduce anything that’s excess, redundant or unnecessary. Rethink management activities such as unnecessary tracking systems, smooth work systems and authoritative systems. Map your value stream to identify areas and steps required for improvement for your organisation. Lean process mapping entails detailing the specific actions that are taken throughout your entire process, enabling you to identify which steps add value or cost you money.
- Amplify learning: introduce and increase feedback loops within your development process. Short feedback loops create meeting points and help you move towards uniformity. When constraints are communicated, solutions can emerge.
- Decide as late as possible, the moment at which failing to decide eliminates an important alternative. Make a list of decisions that need to be made and group them into 2 categories: tough to make and easy to make. Discuss what you would need to make the tough decision easier.
- Decide as fast as possible: customers like rapid delivery, which means less time for customers to change their minds. The key to reducing cycle time (the time it takes to get from one end of the process to the other) is to practise a steady rate of arrival and control of what comes into your queue. Set priorities and select work that is critical.
- Empower your team: let your team design their own working procedures. A manager’s role should be to coach, train and assist where needed. It’s key to understand the fundamental principles that make up practices and transform those principles into new practices. A feedback loop going both ways between managers and workers to drive improvement is vital.
- Build-in integrity: smaller systems should be developed by a single team that has immediate access to the people who will judge the system’s integrity. Customer tests provide excellent customer-development communication, and complex systems should be represented using models and languages that the customer understands and that programmers can use without major refinements. Large systems should have a master developer who has technical credentials and deep customer understanding.
- See the whole: your production system is not just a sum of its parts; it’s a product of those interactions. When systems start to break down, rigid, more sequential rules are usually put in place. A sequential/rigid process may cure one symptom but not the root of the problem. It will become increasingly difficult to keep up with changing needs. To address the root cause, ask yourself the following questions:
- Why were new modules added?
- Why did the new modules generate defects in other modules?
- Why were they not tested?
- Why was there so much pressure?
- Why did you think this process was necessary?
How will my business benefit?
The faster your business can convert a product request to a finished output, the more leverage you have over your competition. Lean manufacturing means less production time, more satisfied customers and an overall decrease in waste. However, it remains important that you analyse the advantages and disadvantages of implementing a lean production system and how it could affect the success of your business.